Kaynak ısısının etkisi ile meydana gelen Çarpılmanın sebebi nedir?
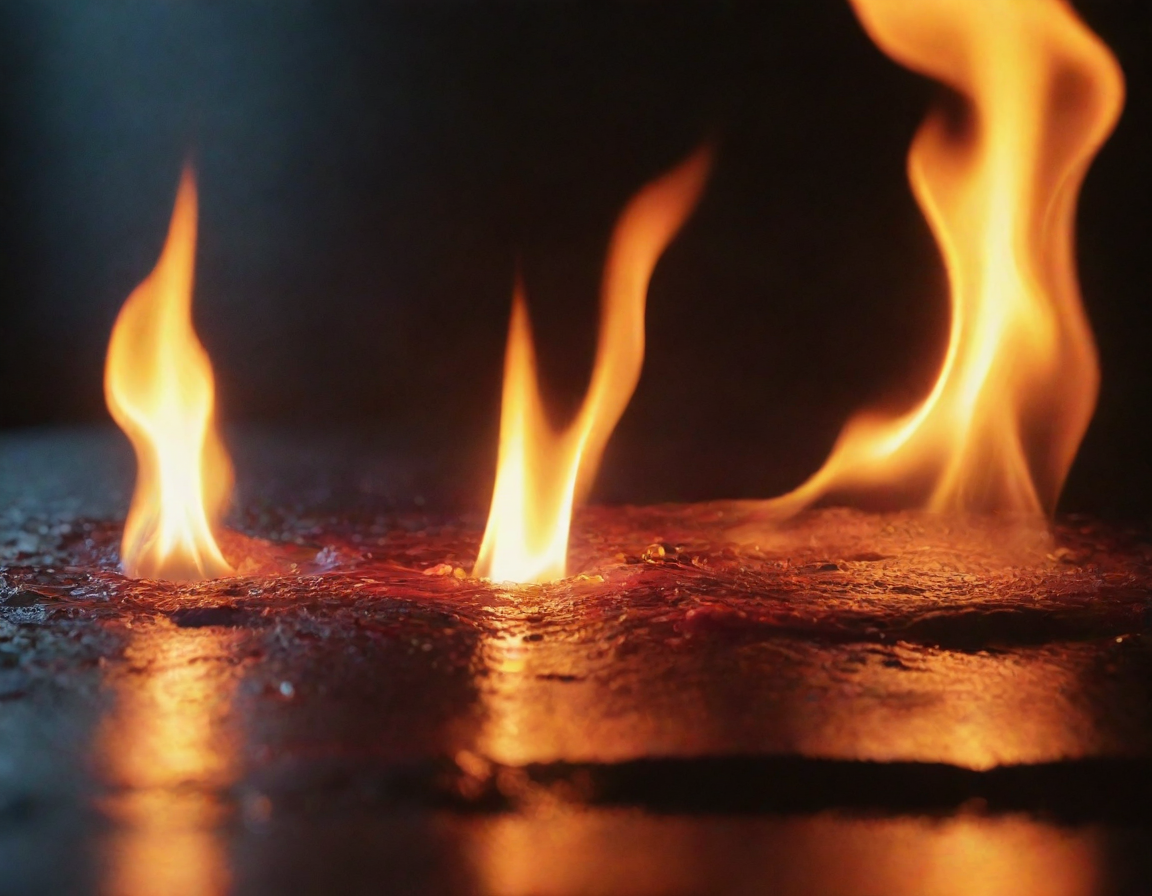
Kaynak ısısının etkisi ile meydana gelen Çarpılmanın sebebi nedir?
Kaynak ısısının etkisiyle meydana gelen çarpılma, metal ve plastik malzemelerin işlenmesi sırasında sıkça karşılaşılan bir sorundur. Bu fenomenin ardındaki fiziksel mekanizmaları anlamak, üretim sürecindeki kaliteyi artırmak ve israfı azaltmak için kritik öneme sahiptir. Peki, çarpılmanın sebepleri nelerdir? Bu sorunun yanıtı, endüstrinin geleceğini şekillendirebilir.
Kaynak Isısının Malzeme Üzerindeki Etkileri
Kaynak işlemleri, yüksek sıcaklıkların malzeme üzerinde meydana getirdiği birçok değişikliği içerir. Kaynak ısısı, özellikle metal ürünler üzerinde önemli etkiler yaratır. Öncelikle, ısının etkisiyle malzemenin kristal yapısı değişir; bu, metalin mekanik özelliklerini etkileyerek, çekme dayanımını, sertlik seviyesini ve tokluk oranını düşürebilir. Kaynak esnasında sıcaklık değişimleri, metalin genişleyip büzülmesine neden olur; bu da malzemenin içindeki gerilmelerin birikmesine yol açar.
Bu gerilmeler, özellikle soğumanın eşit dağılmaması durumunda deformasyonlara neden olur. Çarpılma, bu tür gerilimlerin sonucu olarak ortaya çıkabilir. Yüksek sıcaklıkta ısınan bir malzeme, kaynak sonrası soğurken farklı hızlarda büzülebilir. Bu farklı büzülmeler, malzeme üzerinde istenmeyen gerilmelerin birikmesine ve sonunda çarpılmalara yol açar. Bununla birlikte, kaynak işleminin uygulandığı malzemenin kimyasal bileşimi, ısının etkilerini daha da belirginleştirebilir. Dolayısıyla, kaynak sırasında uygun ısı kontrolü sağlanmadığında, bu çarpılmalar malzemenin işlenebilirliğini ve dayanıklılığını olumsuz etkileyebilir.
Çarpılma Olgusunun Fiziksel Temelleri
Çarpılma olgusu, kaynak ısısının malzeme üzerinde oluşturduğu termal etkilerle yakından ilişkilidir. Bir malzeme kaynak sırasında yüksek sıcaklıklara maruz kaldığında, bu durum iç yapısında genleşme ve soğuma aşamalarında farklı genişleme oranlarına neden olur. Isı, malzemenin belirli bölgelerinde daha fazla genleşmeye yol açarken, diğer bölgelerde soğuma gerçekleşir. Bu farklılık, malzeme içerisinde gerilim birikmesine yol açar.
Gerilimler, malzemenin içinde deformasyon ve denge durumunu bozarak çarpılmalara neden olur. Özellikle kaynak yapılan bölgelerdeki ısı, metalin mikroyapısında değişikliklere sebep olarak, bağlantı yerlerinin mekanik özelliklerini zayıflatabilir. Daha sonra, soğuma süreci başladığında, genleşen malzeme farklı hızlarda geri çekilir; bu da çarpılma olgusunu artırır.
Kaynak sonrası çarpılmalar, özellikle yapıda yapılan testlerde ciddi sorunlar yaratabilir. Bu nedenle, kaynak işlemlerinde ısı kontrolüne dikkat edilmesi, çarpılma olasılığını azaltarak, hem malzeme kalitesini hem de yapının güvenliğini artırmak için önemlidir. Malzeme bilimi ve mühendisliği, bu tür olumsuz etkilerin önüne geçmek adına sürekli olarak gelişmektedir.
Çarpılmanın Önlenmesi ve Yönetimi
Çarpılmanın önlenmesi ve yönetimi, elektrik güvenliği açısından büyük önem taşır. Öncelikle, elektriksel sistemlerde düzenli bakım yapmak, potansiyel tehlikeleri azaltır. Yalıtım, sistemlerin güvenliğini artırarak çarpılma riskini minimize eder. Yalıtım malzemeleri, iletkenlerin dış etkilerden izole edilmesini sağlar.
Çalışanlara yönelik eğitimler düzenlemek de çarpılma riskini düşürür. Elektrik akımına maruz kalma durumunda ne yapılması gerektiği, güvenlik protokolleri hakkında bilgi sahibi olmak, acil durumlarda etkili bir şekilde hareket etmeyi sağlar. Ayrıca, iş yerlerinde uygun kişisel koruyucu ekipman (PPE) kullanımı teşvik edilmelidir. İzole eldivenler, kauçuk botlar gibi ekipmanlar çarpılma riskini önemli ölçüde azaltır.
Elektrik sistemlerinin doğru bir şekilde topraklanması, özellikle yüksek gerilimli sistemlerde hayati öneme sahiptir. Topraklama, elektriğin güvenli bir şekilde yere akmasını sağlayarak potansiyel çarpma durumlarını engeller. Son olarak, elektrikli cihazların ve ekipmanların standartlara uygun olarak üretilmesi, güvenlik seviyesini artırır ve çarpılma risklerini en aza indirir. Bu önlemler, hem iş yerlerinde hem de evde güvenli bir çevre oluşturur.